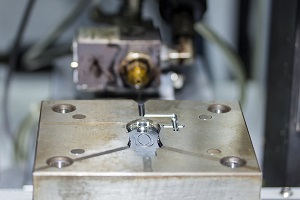
When it comes to your plastic products, the only holes that should exist are the ones on the designs. Like with all manufacturing processes, plastic injection molding can introduce defects into their products. The important thing for the manufacturer and client to do is to detect the defects and then troubleshoot the problems that are causing them. This blog focuses on the two major source of holes – voids and bubbles – in plastic injection molding: vacuum voids and gas pockets.
Vacuum Voids and Sinks
To understand how a vacuum can form in injected plastics, it’s first important to understand how plastic reacts in a mold. When molten plastic is injected into a mold, its performance is affected by four major forces: the pressure pushing it, the temperature it’s at, how well it flows at that temperature, and how quickly it will change temperature (i.e. cooling rate). When these conditions are not optimal, it can cause voids and sinks.
Causes of Vacuum Voids
Vacuum voids and sinks are usually caused when there’s not enough plastic in the mold, and as the plastic cools, it leaves empty spaces as the plastic shrinks. Where the plastic touches the mold, it cools first, meaning the bubble will not be as visible: this is a void. When this shrinking occurs on the surface, it’s a sink defect instead.
Solutions to Injection Vacuums and Sinks
With the need to get more plastic into the mold, several options are available. Most involve dealing with those four forces described above, altering the mold tool or plastics to compensate:
- Higher Pressure and Times: Getting in more plastic through higher injection pressure and second stage (pack and hold) time can get the needed plastic into the mold.
- Runner and Gates: Increasing the runner size and altering the mold gates can bring more plastic into the mold.
- Slower Cooling Rates: Working with the temperature of the plastic or mold can also help. This could be switching to plastics with lower melting points, heated molds, or hot runners.
- Tool Redesign: Sometime, the issues could be with the mold. If parts are too thick, they may be needing a redesign to avoid molds forming when so much plastic shrinks.
While the root cause is related to the injection mold defect of short shots, in that defect the issue is focused on flow and mechanisms of the mold that interferes with that.
How Gas Pockets Form in Plastics
The other way bubbles can form in plastic for the plastic to be pushed out of the way with the formation of gas inside the mold and plastic. When these gases form on the outside they can cause discoloration in the form of splay or “silver streaks.” However, they can also form inside the plastic itself and cause bubbles to form and deform the plastic.
Causes of Gas Pockets
There are four major sources of gas bubbles in plastics, from mechanical to chemical.
- Air: In a plastic injection mold, air must make way for the plastic. With venting problems or poor mold design in the mold, air can become trapped.
- Water: Moisture can enter the mold along with the resin, which is why resin dryers are so important. Water turns to vapor in in the molten plastic and causes gas pockets.
- Volatiles: Certain types of resin can also produce gas when they are heated due to low-boiling point volatiles, which forms as gas.
- Overheating: Finally, certain types of resin or additives can decompose (burn) at higher or longer heats. Not only does this damage the plastics, but it releases gases in the mold.
Troubleshooting Gas Formation in Molds
Dealing with gas formation requires troubleshooting the parts and the mold for the root cause above. Air pockets requires troubleshooting the mold for air-traps and venting issues. For moisture, the above-mentioned dryer can be used or switching to non-hygroscopic polymers. Volatiles and decomposition require looking at the plastics, additives, heat of the injection molding process.
It’s important to make sure the manufacture of your parts is up to the test of producing defect-free plastic injection molding parts. Learn about all the common molding defects and issues in part one and part two of that series, as well as the others featured in this article. Work with an injection molding company that understands the process and tool creation and troubleshooting, like Midstate Mold & Engineering. Contact us to consult on your current project, or you can directly request a quote on any or all of the services you need.