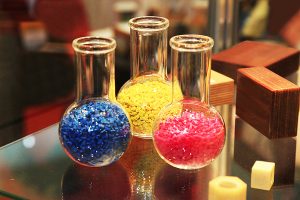
There are a lot of things that go into making plastic parts. But the single biggest choice that will affect multiple categories of strength, price, flexibility, production speed, and even mold design during the project is the kind of plastic resin you pick for your production. It’s also a decision that needs to be made by the client, not the mold or part designer. All we can do is suggest plastics based on your needs. Today we’re here to provide you with some background on the four most popular thermoplastics and why they are so often used.
Acrylonitrile Butadiene Styrene
Also known by the acronym ABS, acrylonitrile butadiene styrene is an opaque polymer that is a versatile and lightweight plastic. It is a thermoplastic (meaning it can be re-melted and reused) and impact-resistant that can be easily mixed with additives to tweak performance. It has largely supplanted high impact polystyrene (HIPS) as the top pick.
Additional Qualities Include
- Temperature Resistant: Resistant to both heat and cold with less negative reactions.
- Heat Morphic: Molded at high temperatures can bring out gloss, and at low temperatures improve resistance and strength.
Overall, ABS is considered a workhorse in the plastics industry. Learn more in this complete writeup: Thermoplastic Highlight: ABS Plastic for Injection Molding.
Polypropylene
Also known as PP, polypropylene is commonly used in packaging and textiles. Its high flexibility makes it an ideal choice for non-loadbearing parts, including working as a living hinge. You will also see it a lot in the textile industry, such as waterproof bags, totes, and gear.
Additional Qualities Include
- Chemically Resistant: Bases and acids don’t react easily with PP, which is why it’s often used in the container of cleaning products.
- High Elasticity: Unlike some plastics, PP has a higher degree of elasticity and will deform instead of breaking.
- Insulation: Polypropylene has a very high resistance to electricity and will often be used in electronics.
Polyethylene
A cousin of polypropylene, polyethylene (PE) comes in multiple types of density due to its variable crystalline structure. Generally speaking, it has a larger range of applications but is a master of none, with a price-point slightly higher than other popular plastics.
Types of Polyethylene
- High-Density Polyethylene (HDPE) is a much more crystalline, making it stronger and more rigid.
- Low-Density Polyethylene (LDPE) is often sheet-thin and used in grocery bags and plastic wrap.
- Ultrahigh Molecular Weight Polyethylene (UHMW) has high-performance applications in the medical field and even ballistic vests.
Polycarbonate
Also known as PC, polycarbonate is the go-to for transparent plastics as a naturally transparent amorphous thermoplastic (similar to glass in light transmission). A robust thermoplastic, PC has a very high impact strength compared to other plastics on this list. A natural UV filter, you can often find it in eyewear.
Additional Qualities Include
- High Deformation Strength: It can be processed and formed at room temperature using sheet metal techniques, such as bending on a brake.
- Construction and Automotive: Due to its high resistance, you can find polycarbonate in both the automotive part and construction material fields.
Of course, this has only scratched the surface of popular thermoplastics and other polymer resins used in injection molding. Several specialty plastics include PEEK (Polyether ether ketone) and PTFE (Teflon) might be needed depending on your market. Here at Midstate Mold & Engineering, we can guide you through the entire process from mold design to parts manufacturing. Contact us today to get started. Make sure to also check out our other blogs on types of plastic for injection molding here and here.