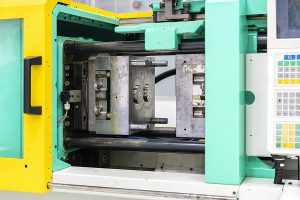
At the heart of the industrial-scale plastic manufacturing known as injection molding machines, is the injection molding press. In these tightly engineered machines, heat, intense pressure, computerized systems, and precise machinery all work together to quickly and efficiently take molten plastic, subject it to high pressure, release, and then set up to do it all again. Understanding this part of injection molding machines can help you be better prepared to work with manufacturers on your products.
The Press of an Injection Molding Machine
While the injection mold—as known as the tool—might be the heart of the injection machine, it can’t work with the press. To follow that metaphor, the press is the muscles that keep the heart beating and the arteries that feed it blood, though here we’re talking about clamping pressures and heating resins. It contains several components to do this:
- The hopper feeds plastics into the machine. This polymer resin typically consists of pellets but can be shavings, flakes, or reprocessed thermoplastics from previous pressings.
- The barrel heats and injects the plastic into the mold. It includes the heating barrel and a rotating screw that feed the now-molten plastic into the mold.
- The platens hold the mold during operation. These hefty clamps are configured to the mold in use, holding both halves of the mold to bring them together and apart again.
- The clamp opens and closes the mold. The clamping force is a critical part of injection molding, needing to be properly calibrated to avoid defects or timely delays.
Learn more about how this process works in our blog, Five Steps of the Thermoplastic Conversion Process.
How Much Pressure Does Your Mold Need?
Every mold needs a different amount of clamping force, usually measured in press tonnage. The factors that go into this include the area of the mold interior plus runners and the type of thermoplastic being used. An additional margin is included for safety. Different injection machines and their presses have different press ratings—for example, a machine with a 70-ton rating provides that amount of pressure to the mold. Generally speaking, larger machines have higher tonnages, so reducing cavity sizes in mold or using plastics that melt more easily can reduce the machine size needed.
Additional Productivity Factors to Consider
While it’s important to consider the press and injection molding machine employed by a manufacturer, it isn’t the only factor that impacts the cost of the produced part.
- The Quality of The Mold: How a mold is designed, made, and maintained plays a significant role in part quality and operation of the mold.
- Standards and Quality Assurance: The standards and QA of the manufacturer can affect the production, part defects, and suitability of the polymer sources.
- Industry 4.0 Technologies: Some of the largest increases in productivity and lower costs come from the use of learning AI systems and enhanced robotics.
At Midstate Mold, we think all of our clients benefit from a better understanding of the systems that go into parts production—and not just because we do it all. By combining our deep knowledge base as mold makers, maintainers, and manufacturers with exacting quality assurance and Industry 4.0 technologies, we’re ready to tackle any project, including in the medical and life science sectors. Learn more by contacting us today or jumping right into a quote.